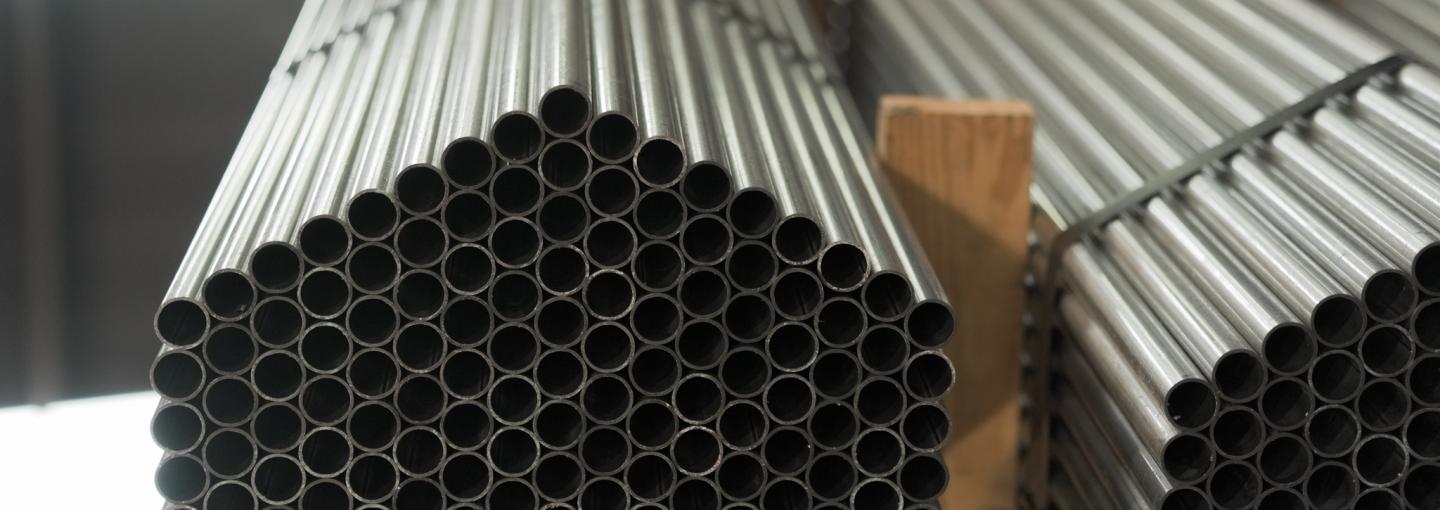
A Brief Overview of our Tube Production Process
Sourcing & Shaping
Gregory sources steel coils from mills with a strip width meticulously controlled to within ± 0.010 inches. All coils come pre-galvanized with a base layer of zinc for enhanced corrosion resistance. Achieving a strong weld requires careful preparation of the strip edges before welding. This involves passing the partially formed strip through a series of rolls called fin passes. The purpose of these fin passes is to burnish the strip edges, ensuring they are clean for welding and properly beveled to allow for even joining. It’s crucial that the strip edges meet without any gaps at the top (outside of the tube) or bottom (inside of the tube). With each series of Fin Passes, the steel gradually assumes the final shape of the tube. This is called “flowering” of the strip.
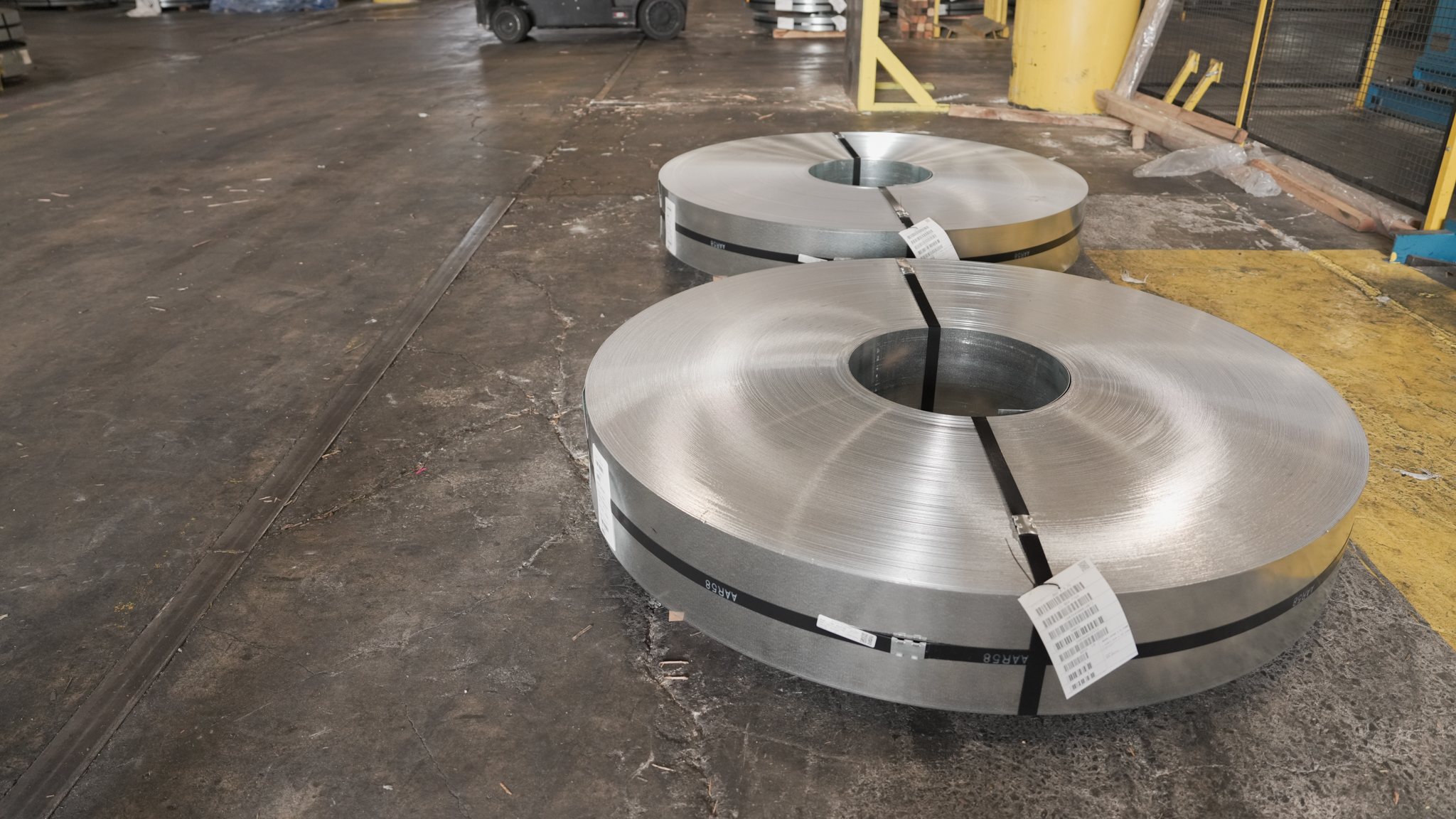
Electric Resistance Welding
Using a high-frequency induction coil, we induce current into the strip through a non-contact process called Electric Resistance Welding (ERW). As the current flows through the coil, it generates a magnetic field around the coil, some of which intersects with the open tube. This interaction creates an electric field on the outer surface of the tube, leading to a voltage difference across the strip’s edges. To focus the current onto the strip’s edges, we use an impeder—a cluster of ferrite rods positioned inside the tube. Concentrating the induced current along the strip edges causes them to heat up. The level of heat and resulting molten metal is controlled by a computer and matched to the steel’s speed. At this stage, the steel passes through weld pressure rolls. These rolls then press the molten strip edges together.
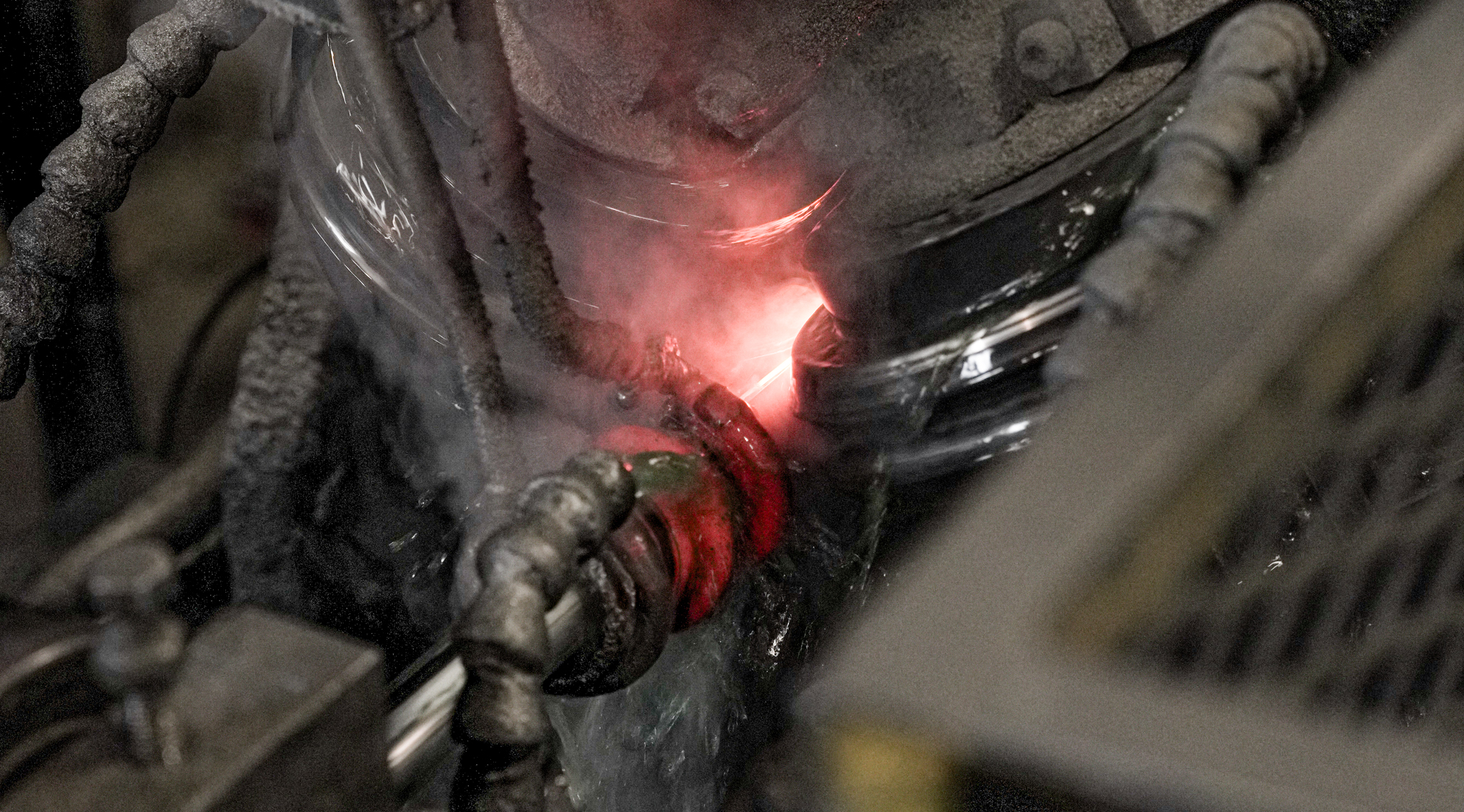
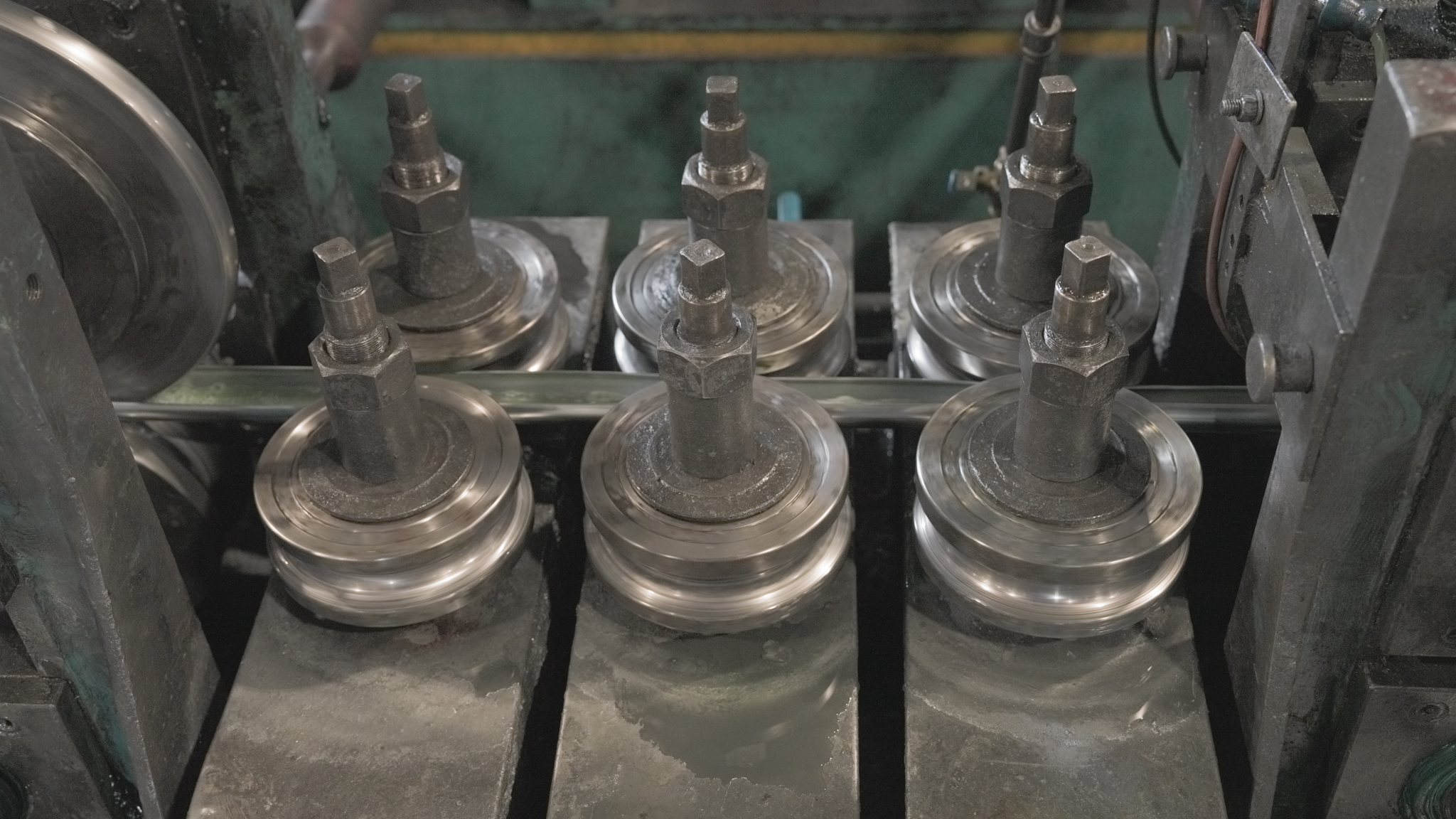
Scarfing
Tube scarfing is the process of removing excess welding material from longitudinally welded tubes. When the strip edges are joined, molten metal is extruded from the top and bottom, creating a metallurgical bond. This extruded metal is then cut from the outside of the tube, leaving a smooth, flush surface. This process is known as bead removal. To remove or smooth the ID weld, a weld seam roller is used. This tool flattens the weld bead, ensuring adequate clearance inside the tube for conveyor applications.

Coating & Cooling
Remetalization refers to the application of zinc coating onto the tube’s surface forming an adherent bond between the weld area and the molten steel. Following the scarfing process, our weld seam equipment applies a precise amount of zinc spray to guarantee sufficient protection against corrosion. The tube is treated with a UV coating, a surface treatment that offers anticorrosive protection and flexibility through ultraviolet radiation. Controlling the cooling rate with precision is crucial to prevent detrimental temperature gradients that may lead to cracking or introduce additional stresses. This controlled cooling of steel is commonly known as quenching and tempering.
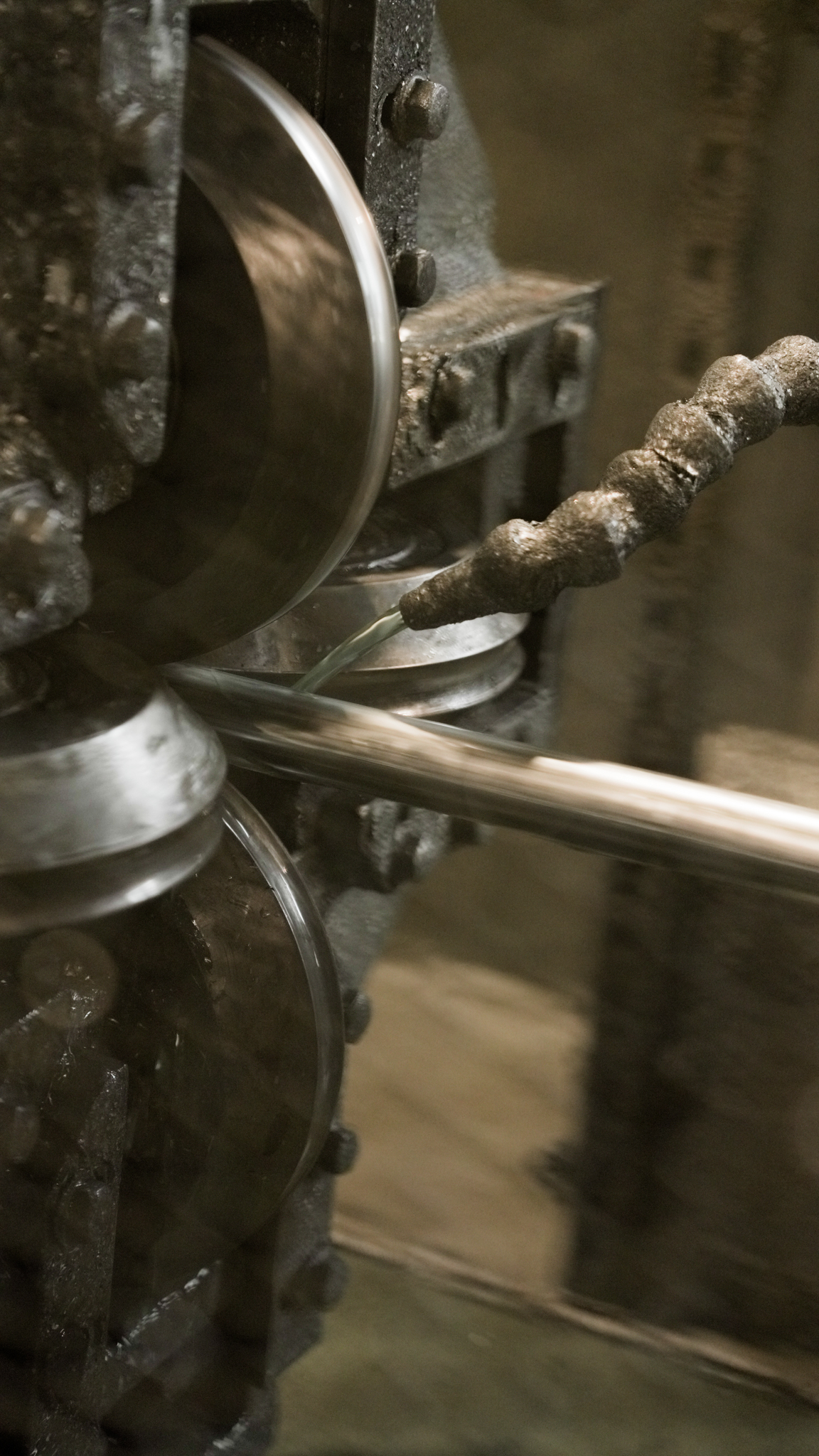
Quality & Testing
Gregory Tube uses a pyrometer to measure the temperature of the weld. Also known as an infrared thermometer, a pyrometer is a non-contact device that measures temperature by detecting an object’s electromagnetic radiation, ensuring the steel is heated sufficiently for welding. Additionally, a destructive test is performed to ensure the quality of weld strength. For each coil, a sample of the finished tube is crushed in each direction relative to the linear weld.
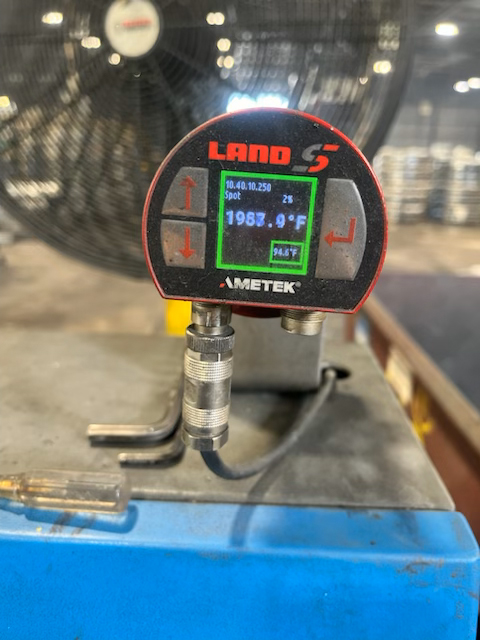
Check out gregorytube.com for more info.